Steel is one of the most important materials that have been invented in the history of construction. Known for centuries, it has allowed mankind to erect huge skyscrapers, bridges, roads or railroads. But why do we still use steel when aluminum offers better corrosion resistance and much lower weight? Let’s find out what supports the popularity of steel in construction.
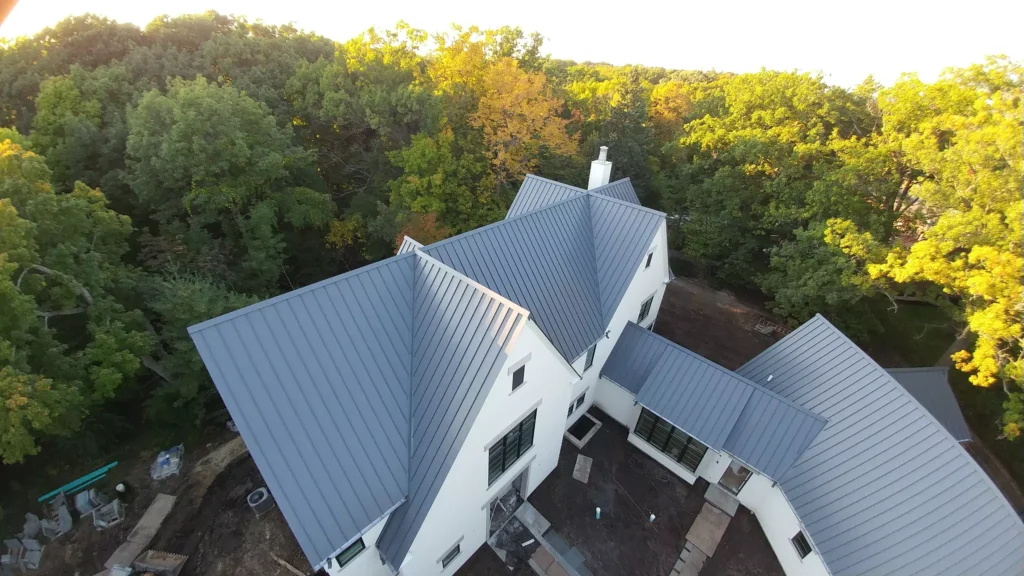
Table of Contents
Although the performance of steel is strongly dependent on its alloy, there are many special characteristics that distinguish virtually all types of steel.
For the purpose of this article, we will focus on S235, S275 and S355 alloys – these are the most popular types of structural steel. At this point you need to know that the S355 alloy is the most durable, but also the most expensive.
Steel is more durable than aluminum
Compared to aluminum, even weak steel alloys have higher tensile and compressive strengths. This parameter is important when metal structural components are to carry heavy loads. The differences between steel and aluminum are illustrated in this table:
Material | Yield strength (Yield) [MPa] | Tensile strength (UTS) [MPa] | Compressive strength [MPa] |
S235 Steel | 235 | 360-510 | 235 |
S275 Steel | 275 | 370-530 | 275 |
S335 Steel | 335 | 470-630 | 355 |
6061 Aluminum | 240 | 310 | 240 |
6063 Aluminum | 145 | 210 | 145 |
6005 Aluminum | 220 | 250-270 | 220 |
At first glance, the data shown in the table is not very impressive. However, if you compare the popular aluminum alloy 6061 and the high-grade steel S335 with each other, you will notice that in order to achieve the same strength, the aluminum support beam must have 50% more surface area and therefore 23% more diameter.
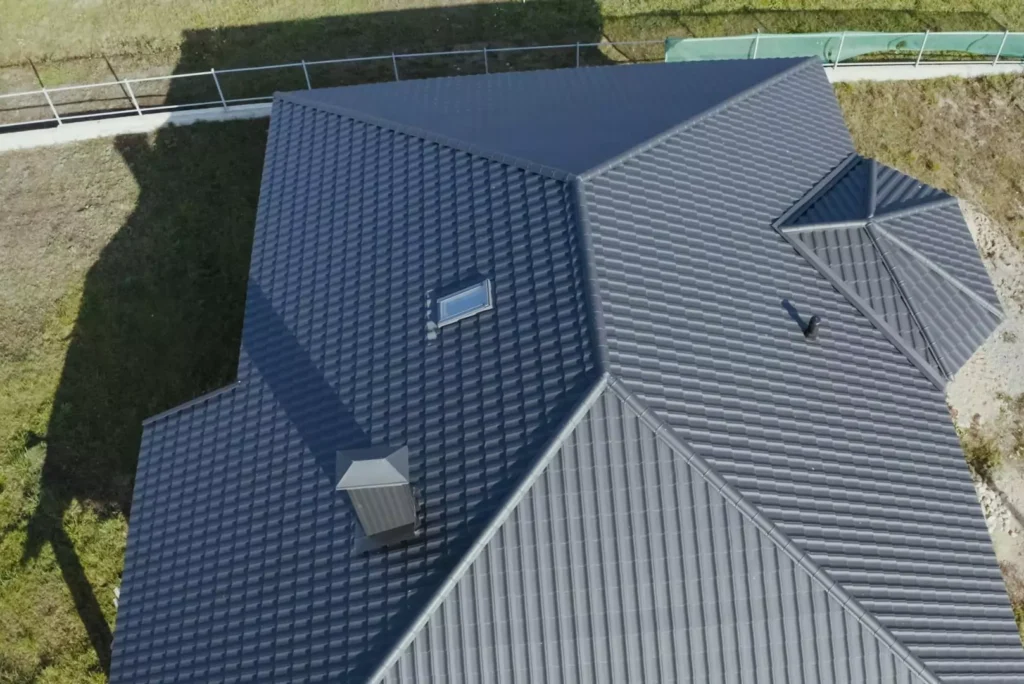
Structural steel is cheaper than aluminum
The price differences between steel and aluminum are huge. The cost of buying a ton of quality S235 structural steel is between $400 and $650, while 6061 aluminum costs about $1,800 – $2,200 per ton.
Even if you are building a relatively small house of 200 square meters (~2,200 sqft), you will need about 3 tons of steel – that’s how much is needed to prepare the reinforcement for the concrete. Although the consumption of aluminum would be slightly less, we are still talking about a difference in purchase price of more than $3,000, and with that the performance of such a structure would be slightly worse.
However, if you are building something on a larger scale, the cost differences are even greater. For the Varso Tower, the tallest building in the European Union, 14,000 tons of steel were used. The construction of the Burj Khalifa, on the other hand, used about 50,000 tons of this material. If all the structural elements used in these projects were to be made of aluminum, Varso Tower would be about $20,000,000 more expensive, while Burj Khalifa would be $70,000,000 more expensive.
Aluminum is very rarely used in construction precisely because of its very high prices – high weight in many cases is not a problem, but high price is.
Processing and welding of steel is easier and faster
The processing of building materials is a very important criterion. First, the simpler it is, the lower the cost of purchase. Second, the ease of drilling, welding, riveting and cutting makes the process of erecting a building faster, and this also translates into the final cost of all new construction.
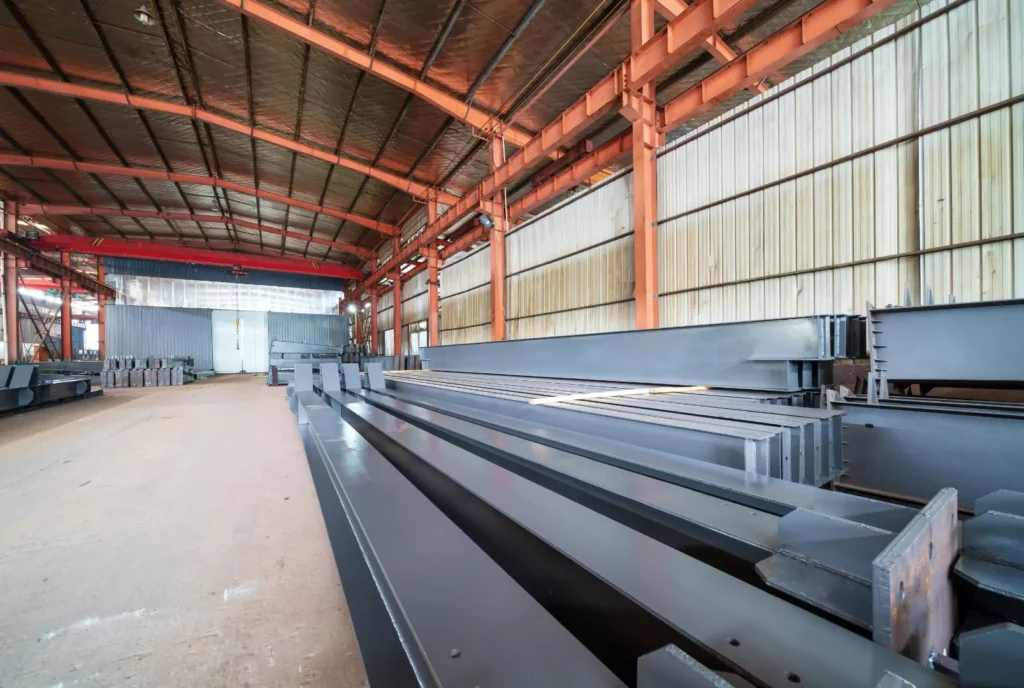
From a technological perspective, the biggest challenge is welding aluminum – due to its much lower melting point, higher thermal conductivity and less fusible oxide collecting on the surface, it is a difficult process. Aluminum requires more precision and much faster welding. Iron-based alloys are simply easier to work with, which is important if you are erecting a large building with multiple floors or a large area.
Reducing the time it takes to build a house is crucial for builders these days – with the price of labor rising, everyone is looking to speed up all construction processes.
Steel is more accessible than aluminum
Year after year, more and more materials in the construction industry are being recycled, obviously driven by the desire to cut costs.
While the process of remelting aluminum as well as ferrous metals is not a major problem, the availability of scrap metal can already be a real obstacle. Due to its price and greater durability, the supply of aluminum on the secondary market is limited, especially in countries with lower levels of economic development. This, of course, makes obtaining large quantities of the metal a real problem.
Our observations also show that steel is produced in more places around the world – you can find iron alloy mills in virtually every country, while the group of aluminum producers is more limited, due to the energy-intensive nature of its processing. The distance from the manufacturer to the end customer, of course, has a big impact on the price, as metal bars, sheets, beams and other structural elements have to be transported later using trucks.
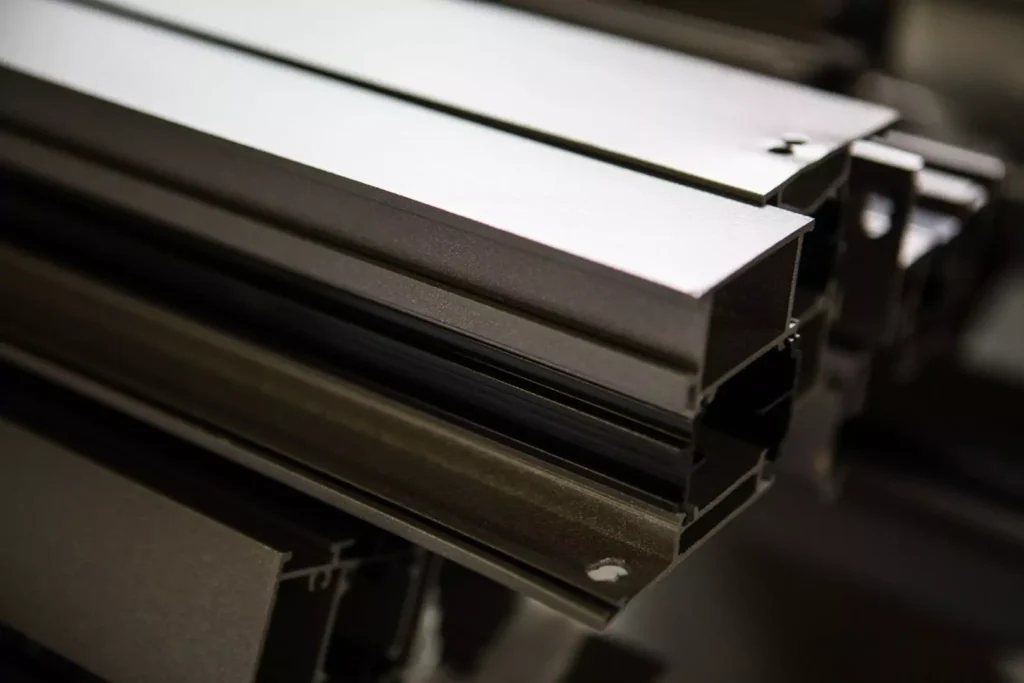
Anti-corrosion properties are not that important
One of the biggest advantages of aluminum is its very high resistance to corrosion. Although it gets covered with a layer of oxide, this process does not fundamentally affect the mechanical performance of the oxidized component. This is very important in the automotive, aerospace, marine or plumbing industries, but not necessarily when we are talking about rebar that is cast in concrete.
In most cases, the anti-corrosion properties of aluminum are simply irrelevant, since structural elements of buildings are usually not exposed. With the development of metal surface preservation techniques and advances in materials science, it has also been possible to obtain steel that is resistant to rust even in environments with high saturation of seawater. As a result, paying up to three times the price for aluminum has lost any sense.
Recommended for you: Top 5 innovative wall construction technologies you should know about
Recommended for you: How Long Does It Take to Build a House?